On February 7, the Occupational Safety and Health Administration (OSHA) issued a reminder to employers to protect employees from workplace carbon monoxide (CO) risks, particularly those associated with wintertime use of portable generators and heating equipment inside enclosed spaces. That reminder includes links to OSHA’s “Carbon Monoxide Fact Sheet,” which outlines hazards and appropriate employer responses. The rest of this note discusses OSHA’s explanation of these risks and how to manage them.
What are the risks of CO exposures in enclosed spaces?
Carbon monoxide is a colorless, odorless and toxic gas that is produced by incomplete combustion of carbon-based fuels and materials, including natural gas and diesel. When inhaled, it displaces oxygen in the blood and so deprives the heart, brain, and other vital organs of oxygen. The severity of exposure symptoms increases with the extent and duration, and varies among individuals. Prolonged or high exposures can cause headaches, dizziness, drowsiness, nausea, vomiting or tightness across the chest. Extreme exposures can lead to neurological damage, coma and even death. Exposed individuals removed from the source will shed the molecules, although acute poisoning may produce irreversible damage.
These risks increase when workers spend extended time in enclosed or semi-enclosed spaces, where CO can accumulate. Some risks are always present in spaces where combustion occurs. CO is produced when fuel combusts in powered tools, compressors, pumps, welding equipment, furnaces, forklifts and motorized vehicles. In cold weather employers may add portable heaters and even portable generators and similar equipment, while simultaneously “tightening” workspaces by closing windows and reducing external ventilation.
OSHA identifies the following locations and workers as particularly at-risk:
- Locations: boiler rooms, warehouses, petroleum refineries, pulp and paper production, and steel production; around docks, blast furnaces, or coke ovens
- occupations: welder, garage mechanic, firefighter, carbon-black maker, organic chemical synthesizer, metal oxide reducer, longshore and marine terminal worker, diesel engine operator, forklift operator, toll booth or tunnel attendant, customs inspector, police officer, or taxi driver
What preventive steps should employers and employees undertake?
To reduce the chances of workplace CO poisoning, OSHA recommends that employers take the following actions:
- Install an effective ventilation system that will remove CO from work areas.
- Maintain equipment and appliances (e.g., water heaters, space heaters, cooking ranges) that can produce CO in good working order to promote their safe operation and to reduce CO formation.
- Consider switching from fuel-fired equipment to equipment powered by electricity, batteries, or compressed air.
- Prohibit the use of gasoline-powered engines or tools in poorly ventilated areas.
- Provide personal CO monitors with audible alarms if potential exposure to CO exists.
- Test air regularly in areas where CO may be present, including confined spaces (OSHA’s permissible exposure level (PEL) for CO is 50 parts per million as an 8 hour average; rules for maritime industry employers require employee removal from an enclosed space when CO concentration exceeds 100 ppm).
- In areas with high CO concentrations (i.e., atmospheres immediately dangerous to life and health) use a full-facepiece pressure-demand self-contained breathing apparatus (SCBA) certified by the National Institute for Occupational Safety and Health (NIOSH), or a combination full-facepiece pressure demand supplied-air respirator with auxiliary self-contained air supply
- Use respirators with appropriate canisters, in conjunction with personal CO monitoring, for short periods under certain circumstances where CO levels are not exceedingly high.
- Educate workers about the sources and conditions that may result in CO poisoning as well as the symptoms and control of CO exposure.
In addition, if employees are working in confined spaces where the presence of CO is suspected, the employer must ensure that workers test for oxygen sufficiency before entering (i.e., in compliance with OSHA’s Confined Space Standard).
OSHA also recommends attention and additional actions by employees to reduce the chances of CO poisoning in the workplace:
- Report any situation that might cause CO accumulation to the employer.
- Be alert to ventilation problems — especially in enclosed areas where gases of burning fuels may be released.
- Report promptly complaints of dizziness, drowsiness, or nausea.
- Avoid overexertion if CO poisoning is suspected, and leave the contaminated area.
- If an employee gets sick, they should tell their doctor about possible CO exposure.
- Avoid the use of gas-powered engines, such as heaters and forklifts, while working in enclosed spaces.
How should employers and employees respond to possible poisonings?
When CO poisoning is suspected, OSHA notes that the following actions can save lives:
- Move the victim immediately to fresh air in an open area.
- Call 911 or another local emergency number for medical attention or assistance.
- Administer 100 percent oxygen using a tightfitting mask if the victim is breathing.
- Administer cardiopulmonary resuscitation if the victim has stopped breathing.
OSHA cautions that rescuers may be exposed to fatal levels of CO poisoning in a rescue attempt (e.g., if someone has passed out). Rescuers should be skilled at performing recovery operations and using recovery equipment. OSHA also cautions that employers ensure that rescuers are not exposed to dangerous CO levels during rescue operations
What happens next?
OSHA’s reminder is intended to focus employer attention on the risks of combustion sources in enclosed spaces, which can increase during winter cold.
Self-Assessment Checklist
Do any of organization’s workplaces use fueled equipment in enclosed areas – for heating, equipment operation, or processes?
Does the organization make use of temporary heaters for space conditioning, whether on an ongoing/permanent basis or temporarily during cold weather?
If so, has the organization evaluated the risk of CO accumulations in workplaces atmospheres that could endanger workers and other occupants?
- General workplace evaluation (configuration, equipment use, activities)
- Workplace atmosphere monitoring
If so, has the organization implemented training, equipment and/or procedures to ensure that workplace CO levels remain below hazardous levels?
Where can I go for more information?
● OSHA, “Carbon Monoxide Poisoning” factsheet
● NIOSH Carbon Monoxide webpage
About the Author
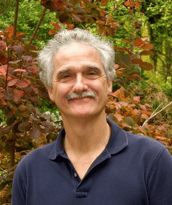
Jon Elliott is President of Touchstone Environmental and has been a major contributor to STP’s product range for over 30 years.
Mr. Elliott has a diverse educational background. In addition to his Juris Doctor (University of California, Boalt Hall School of Law, 1981), he holds a Master of Public Policy (Goldman School of Public Policy [GSPP], UC Berkeley, 1980), and a Bachelor of Science in Mechanical Engineering (Princeton University, 1977).
Mr. Elliott is active in professional and community organizations. In addition, he is a past chairman of the Board of Directors of the GSPP Alumni Association, and past member of the Executive Committee of the State Bar of California's Environmental Law Section (including past chair of its Legislative Committee).
You may contact Mr. Elliott directly at: tei@ix.netcom.com