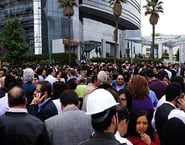
Even if your organization is not required to do so, you should consider the benefits or being prepared to conduct emergency responses and evacuations. Well-developed emergency plans and proper employee training (so employees understand their roles and responsibilities) likely will result in fewer and less severe employee injuries and less structural damage to the facility during emergencies. A poorly prepared plan, on the other hand, likely will lead to a disorganized evacuation or emergency response, exacerbating confusion, injury, and property damage.
Which Employers Require An EAP?
The following OSHA Standards require you to prepare an EAP as part of your compliance with their requirements:
-
Process Safety Management Standard
-
Hazardous Waste Operations and Emergency Response (HAZWOPER) Standard – under specified circumstances
-
Portable Fire Equipment Standard – under specified circumstances
-
Fixed Fire Suppression Systems Standard – under specified circumstances
-
Grain Handling Facilities Standard
-
Ethylene Oxide Standard
-
4,4’-Methylenedianiline Standard
- 1,3-Butadiene Standard
If your organization has workplaces subject to these standards, then it must have EAPs there. Otherwise, the choice is yours.
What Do EAPs Require?
Your EAP must include the following:
-
Preferred methods for reporting fires and other emergencies
-
Emergency escape procedures, including different evacuation scenarios
-
Emergency escape route assignments for employees (OSHA provides separate standards for “exit routes”)
-
Procedures for employees assigned to operate critical plant operations before they evacuate
-
Procedures to account for all employees after emergency evacuation
-
Rescue and medical duties and procedures for designated employees
- Names or regular job titles of persons or departments to contact for further information or explanation of duties under the plan.
You must also establish an employee alarm system that meets OSHA requirements. If you use an employee alarm system to alert fire brigade members or for other specific purposes, each type of alarm must use a distinctive signal.
Except for scenarios required by the specific standards identified above, employers can decide which types of events to cover. For example, different areas are prone to different natural disasters – earthquakes, floods, tornados, etc. If a workplace includes chemicals that could trigger disastrous emergencies, then an EAP should include one or more “hazmat” scenarios.
In addition, you should consider combining your EAP with related planning requirements provided by other laws and regulations. These might include:
-
Other OSHA Standards, such as the Hazard Communication Standard (HCS) and HAZWOPER Standard.
-
Non-OSHA requirements, such as fire code Hazardous Materials Management Plan requirements, and hazardous waste management (contingency plan) requirements. You should consider Integrated Contingency Plan (ICP) Guidance developed by the National Response Team (NRT; which includes OSHA, the Environmental Protection Agency, and other agencies).
What EAP Training Is Required?
The employer must designate and train enough people to assist in the safe and orderly emergency evacuation of employees. OSHA’s guidance refers to these evacuation assistance personnel as evacuation wardens, and recommends that the employer assign one for each 20 employees. OSHA also recommends that these wardens be trained in the complete workplace layout and the various alternative escape routes from the workplace. All wardens and fellow employees should be made aware of handicapped employees who may need extra assistance, such as using the buddy system, and of hazardous areas to be avoided during emergencies. Wardens should also be trained to check rooms and other enclosed spaces in the workplace for employees who may be trapped or otherwise unable to evacuate the area, and then to account for or otherwise verify that all employees are in the safe areas.
In addition, the employer must review your EAP with each employee:
-
Initially when the EAP is developed.
-
Whenever a new employee is assigned to the area, or an existing employee’s responsibilities or designated actions under the EAP change.
- Whenever the EAP is changed.
Furthermore, you must review with each new employee those parts of the EAP he or she must know for self-protection in an emergency.
Is The EAP Written?
Most EAPs must be written. However, if a workplace has 10 or fewer employees, OSHA does not require you to develop a written EAP. Instead, you may orally communicate your EAP to employees. If your EAP is written, you must keep it at the workplace and make it available for employee review.Self-Assessment Checklist
Does the organization implement an EAP in any of its workplaces?
-
As part of required compliance with another OSHA standard?
-
As part of integrated compliance with multiple emergency planning and response requirements (OSHA and/or other agencies)?
- Voluntarily?
Does each EAP meet requirements set forth in OSHA’s EAP standard?
Where Can I Go For More Information?
-
OSHA Evacuation Plans and Procedures eTool webpage
-
OSHA Emergency Preparedness and Response webpage
-
FEMA National Incident Response System webpage
-
National Response Team webpage
Specialty Technical Publishers (STP) provides a variety of single-law and multi-law services, intended to facilitate clients’ understanding of and compliance with requirements. These include:

About the Author
Jon Elliott is President of Touchstone Environmental and has been a major contributor to STP’s product range for over 25 years. He was involved in developing 12 existing products, including Environmental Compliance: A Simplified National Guide and The Complete Guide to Environmental Law.
Mr. Elliott has a diverse educational background. In addition to his Juris Doctor (University of California, Boalt Hall School of Law, 1981), he holds a Master of Public Policy (Goldman School of Public Policy [GSPP], UC Berkeley, 1980), and a Bachelor of Science in Mechanical Engineering (Princeton University, 1977).
Mr. Elliott is active in professional and community organizations. In addition, he is a past chairman of the Board of Directors of the GSPP Alumni Association, and past member of the Executive Committee of the State Bar of California's Environmental Law Section (including past chair of its Legislative Committee).
You may contact Mr. Elliott directly at: tei@ix.netcom.com.
photo credit: Evac After the Earthquake via photopin (license)