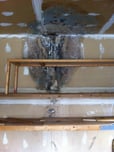
Organizations with facilities that may be subject to routine water infiltration or leaks, or sudden flooding from hurricanes or other events – should consider both sets of information.
Mold Basics
Molds and other fungi are both ubiquitous and plentiful--they have been estimated to make up a quarter of all the biomass on the planet. Molds are found almost everywhere, and can grow on just about any surface, as long as moisture and oxygen are available.
They have been recognized to be potentially toxic to humans and animals for many centuries, although until recently the focus of health concerns has been on ingestion of poisonous mushrooms and molds. However, inadequate air-handling systems in many of the “tighter” buildings constructed since the energy crisis of the 1970s have supported enough mold growth to produce indoor air quality hazards. These have included outbreaks of so-called “building-related illnesses (BRIs)” including allergic reactions, respiratory problems and hyper-sensitivity – extreme examples are often called “sick building syndrome.” Mold infestations in buildings can also cause structural damage to the buildings and their finishings and furnishings.
Preventive measures generally consist of maintaining dry surfaces with adequate air circulation. Remediation involves restoring those conditions, and removing water-saturated materials and identifiable mold. EPA focuses on areas that have just suffered flooding or other immersion, while OSHA addresses saturated and contaminated areas whether from chronic water intrusion or sudden soaking.
OSHA’s Recommendations
OSHA has not adopted a specific standard addressing mold hazards in workplaces, but does apply the General Duty Clause if such infestations can be considered a “recognized hazard” (I wrote about that clause here). Readers with operations in California should note that the state Division of Occupational Safety and Health (CalOSHA) includes a provision in its general workplace Sanitation Standard requiring employers to correct “uncontrolled accumulations of water,” including those from intrusion of exterior water or leakage of interior water, “because of the potential for these conditions to cause the growth of mold” (8 CCR 3362(g))
OSHA and other worker protection and health agencies also provide guidelines to help employers (and managers of residential buildings) evaluate and remediate mold infestations. OSHA has issued extensive guidance covering the following:
-
Mold characteristics and growth
-
Health effects
-
Prevention measures (focused on maintenance operations to prevent accumulations of humidity, moisture and water, and on maintaining air circulation and air duct hygiene)
-
Remediation planning elements and implementation, subdivided to cover four levels of contamination:
-
Level I (small isolated areas)--no more than 10 square feet
-
Level II (mid-sized isolated areas)--10 to 30 square feet
-
Level III (large isolated areas)--30 to 100 square feet
-
Level IV (extensive contamination)--more than 100 square feet of contiguous contamination
-
-
Personal protective equipment (PPE) for remediation workers, including gloves and goggles, and respiratory protection if necessary
-
Sampling for mold (initial, project-related, and after project)
-
References and resource materials.
EPA’s Recommendations
EPA’s has long provided indoor air quality recommendations, which the agency has now supplemented with suggestions for post-flood cleanup activities. These focus on the need to remove contaminated materials and to reduce moisture and humidity. EPA points out that serious long-term health risks can be generated by standing water and wet materials, which provide breeding grounds for microorganisms, such as viruses, bacteria and mold. Accordingly, EPA emphasizes the need to consider replacement of saturated flooring after flooding.
Self-Assessment Checklist
Do the organization’s operations and maintenance (O&M) programs at its facilities including:
-
Inspection and O&M activities designed to minimize the accumulation of moisture at locations within facilities?
-
Programs to identify, evaluate and remediate mold infestations?
Does the organization own or operate any facility in areas prone to flooding from precipitation runoff including from hurricanes?
-
If so, has the organization established hurricane preparedness and response plans for each such facility?
Where Can I Go For More Information?
-
OSHA’s Mold safety and health topic portal
-
EPA’s mold information portal
-
EPA, “A Brief Guide to Mold, Moisture, and Your Home” (2012)
-
Specialty Technical Publishers (STP) provides a variety of single-law and multi-law services, intended to facilitate clients’ understanding of and compliance with requirements. These include:
-
A range of MACT Standard guide
About the Author
Jon Elliott is President of Touchstone Environmental and has been a major contributor to STP’s product range for over 25 years. He was involved in developing Environmental Compliance: A Simplified National Guide and The Complete Guide to Environmental Law.
Mr. Elliott has a diverse educational background. In addition to his Juris Doctor (University of California, Boalt Hall School of Law, 1981), he holds a Master of Public Policy (Goldman School of Public Policy [GSPP], UC Berkeley, 1980), and a Bachelor of Science in Mechanical Engineering (Princeton University, 1977).
Mr. Elliott is active in professional and community organizations. In addition, he is a past chairman of the Board of Directors of the GSPP Alumni Association, and past member of the Executive Committee of the State Bar of California's Environmental Law Section (including past chair of its Legislative Committee).
You may contact Mr. Elliott directly at: tei@ix.netcom.com
photo credit: nusitegroup IMG_0808 via photopin (license)